VDL Fibertech Industries introduces lightweight recycled thermoset composites
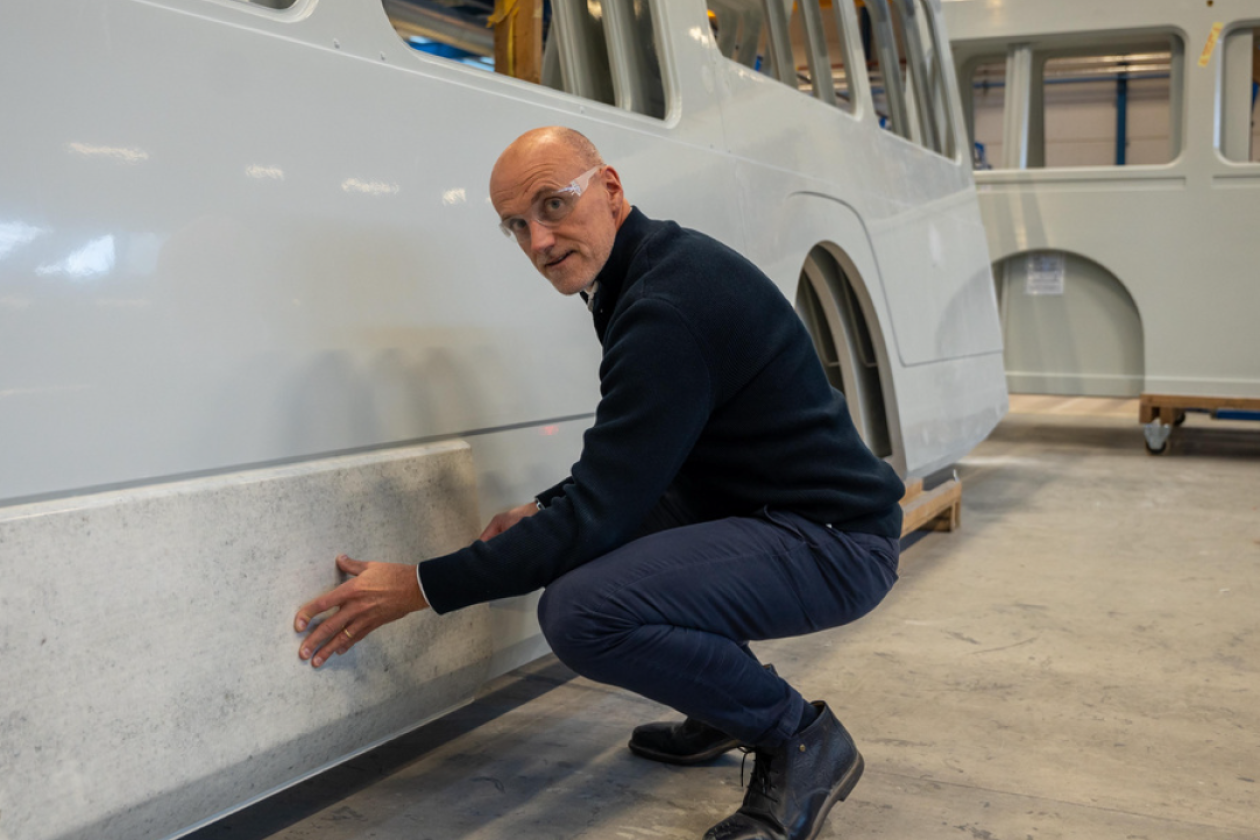
VDL Fibertech Industries has taken a significant step in the development of sustainable composite materials. In collaboration with the Professorship for Polymer Engineering at Windesheim University of Applied Sciences, VDL has developed an innovative method to reuse End-of-Life (EoL) thermoset composites. This presents new opportunities for lighter and more sustainable applications in sectors such as the transport industry.
The challenge of thermoset composites
Thermoset composites, found in products such as wind turbine blades, polyester ship hulls, and train and bus walls, are difficult to recycle compared to thermoplastics. Traditionally, this material ends up in landfills or is incinerated. However, Windesheim has developed a process that reduces the material into small reinforcement elements in the form of flakes with a high length-to-diameter ratio. These flakes are then bonded with new resin to create new composite products.
From heavy infrastructure to lightweight applications
Until now, recycled composites have primarily been used in heavy infrastructure applications such as sheet piling and bridge decking. However, VDL Fibertech Industries is focusing on innovative applications in the transport sector, such as lightweight bus side panels. This project was made possible by the EU-funded MC4 project, in which Windesheim and VDL collaborated to find solutions for composite production waste.
Improving material properties
The recycling process still faces challenges, such as the strength of the material after shredding. Niels van Beek, Sales Manager at VDL Fibertech Industries, emphasizes that fiber length is crucial for the strength of the final product. Thanks to optimizations in collaboration with Windesheim, such as improved moisture resistance and mechanical strength, the material is perfectly suitable for less structural applications, such as skirts under buses.
Scaling up production and future prospects
VDL has made significant investments in expanding its production facility in Hapert, with a new automated production line capable of producing side panels for 1,200 buses per year. This lowers production costs and increases efficiency. However, the biggest challenge for scaling up remains the continuous availability of recycled material. VDL is therefore actively engaging with parties such as the Dutch Railways (NS) to further expand application possibilities.
Conclusion
VDL Fibertech Industries' innovative approach demonstrates that circular economy and high-quality applications can go hand in hand. With further investments and optimizations, recycled thermoset composite can become a sustainable and economically viable solution for various industries.
Stay tuned for more updates on sustainable innovations in the composite industry!